The United States requires a Swift and Affordable Housing Solution. Steel magnate Barry Zekelman is placing a $1 billion bet that his family's fortune can produce prefabricated apartment complexes to meet this demand.
Are Factory-Manufactured Multi-Unit Residences Capable of Alleviating America's Housing Predicament?
It's a scorching 108 degrees in mid-afternoon in the Phoenix suburb of Chandler, and steel tycoon Barry Zekelman is guiding us through his housing factory. At one end, hollow structural steel from one of Zekelman's steel plants enters, while at the other, the "modules" for the apartment complexes exit. Zekelman points to an area where the steel is neatly arranged, already cut into the appropriate sizes for easy retrieval by workers.
"It's like a puzzle," he says. "You've seen construction sites where you had to measure it and cut it again. We cut it like a puzzle. No one's got to measure."
Assembly of apartments inside an air-conditioned factory is more efficient than traditional construction, especially given the intense heat. The modules will eventually be assembled into three- and five-story apartment complexes, primarily in the southwest. The concept is not new. Sears offered prefabricated homes in its catalog over a century ago. While there have been some modest successes, there have also been notable failures, most recently SoftBank-backed Katerra, which expended $2 billion before filing for bankruptcy in 2021.
One major hurdle: Factories demand substantial capital investments, but construction is cyclical by nature, leading to a mismatch. Furthermore, the real estate industry is highly localized, with nearly every town having unique preferences, cost structures, and regulations, making standardization difficult. "I'm sure you've heard the joke that modular has been 10-15 years away for the last 75 years," says Greg Smithies, a partner at Fifth Wall and co-head of its climate technology investment team. Despite the challenges, today even giant real estate developers like Greystar are exploring modular construction.
Zekelman, aged 57 and worth $3.4 billion by Our Website estimates, has been fine-tuning his business model for the past eight years and is now taking a bold step as a builder, developer, and owner of modestly-priced apartment complexes. It's a significant shift from the commodity business in which he built his fortune. However, Zekelman believes that a housing factory is not unlike a steel tubing factory, and factory-built homes can be constructed more affordably and quickly than traditional construction. An additional benefit is labor: By hiring factory workers, Z Modular relies less on construction contractors, who have been in short supply, causing delays in housing projects nationwide.
Climate change has been causing hurricanes and extreme temperatures, and Z Modular's steel-based construction may offer an additional advantage. Zekelman claims that Arizona's apartment complexes have more efficient heating and cooling systems, vitally important during temperatures exceeding 100 degrees, than traditional construction. They may also withstand storms and, specifically, fires better than wooden construction, giving Zekelman a durability advantage and, potentially, a reduction in insurance costs.
Since launching Z Modular as a subsidiary of his family's steel $4 billion (revenue) steel company, Zekelman Industries, in 2016, Zekelman has invested $1.2 billion in the project. "I love it when people tell me what I can't do or that's not how it's done," he says. "I'm a contrarian. I'm like, 'Well, why not?'"
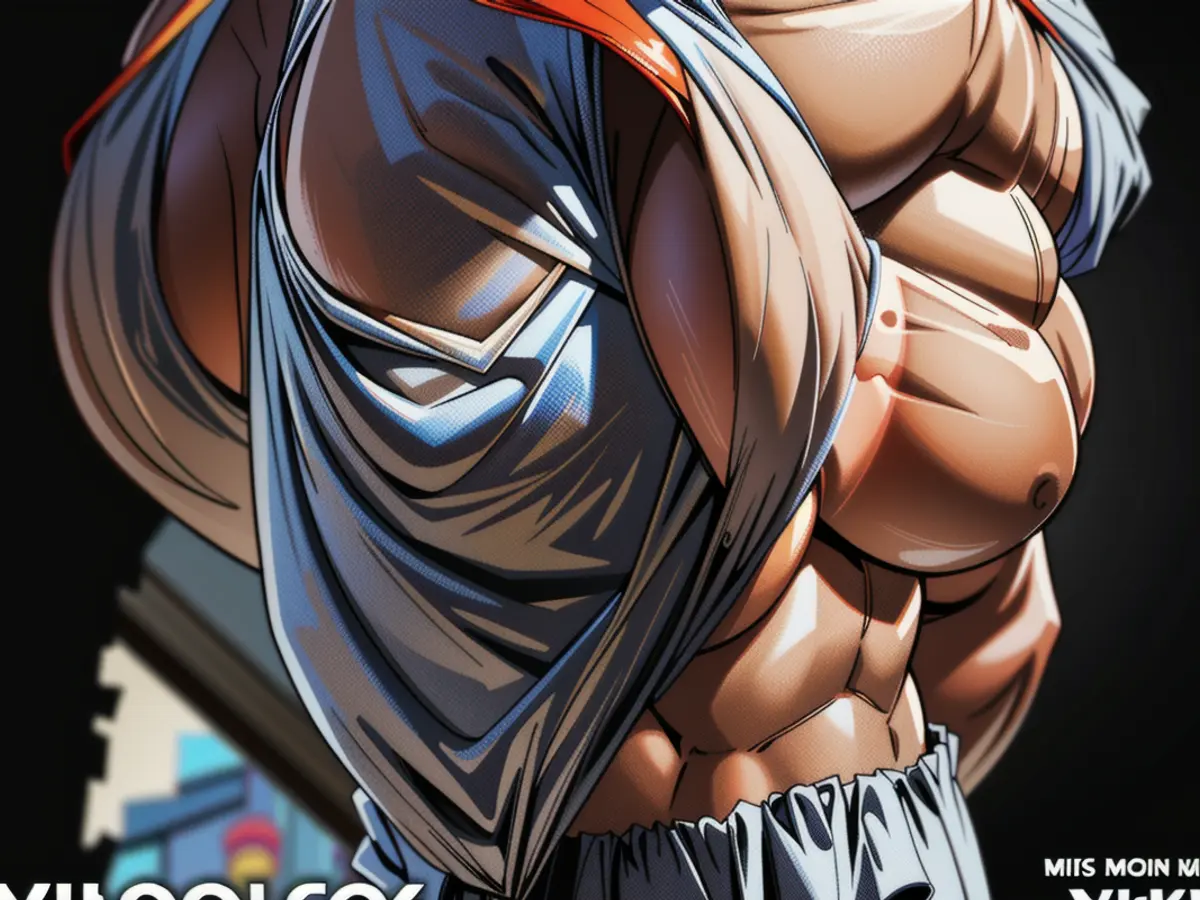
To date, Z Modular has constructed three factories in Killeen, Texas, Birmingham, Alabama, and Chandler, with plans to expand. They have built nine apartment complexes (with 2,245 units) and are slated to complete an additional 15 (with 3,858 units) by the end of 2025. Zekelman estimates that Z Modular (which has been operating at a loss since its inception) generated between $3 million and $4 million in revenue last year once its apartment complexes began renting out units. He expects rental income to reach $20 million this year and $50 million next year as the number of modestly-priced apartments increases.
This business is extremely capital-intensive and even Zekelman's wealth may not be sufficient to support his expansion plans. He is considering whether to take Z Modular public or partner with a REIT or private-equity firm to raise funds for the construction of tens of thousands, or potentially even millions, of apartments. "Hopefully, I can be that pied piper, and everyone will believe in my story and want to be part of it," he says. "I've done it before, and I want to do it again. I think this is a bigger opportunity than my steel tubing business ever could be."
Zekelman's steel business traces back to his father, Harry, a Jewish immigrant from Poland who arrived in Windsor, Ontario, via a displaced persons' camp in Italy. The elder Zekelman was an entrepreneur with ventures including electrical-box manufacturing and industrial real estate.
His dad experienced health issues, and, in 1986, he passed away unexpectedly. The steel tubing business was in the red with revenue of only $1.5 million. It would have been simple to shut it down and claim a tax loss. Instead, Zekelman, aged 19 and a freshman at York University, abandoned his studies to run the company with his older brother. (His younger brother, then in high school, later joined the business.)
"I thrive on challenges," he declares. "I have a knack for enjoying crises because I derive pleasure from resolving them. At times, I manufacture problems so I have something to tackle. If everything is functioning smoothly and flawlessly, I'd disrupt it. I can't just sit idly."
By offering incentives to work faster and boost sales quotas, the younger generation managed to turn around the business. In 1992, they pooled together $16 million to invest in a cutting-edge machine. This gamble paid off as the new equipment enabled the business to operate more swiftly and economically, with minimal inventory.
Adventure-seeker Zekelman, who enjoys boat racing, car racing, scuba diving, and heli-sledding, and has christened all his yachts 'Man of Steel', purchased his latest superyacht - a 282-foot vessel equipped with a dance floor and two swimming pools - from Steven Spielberg for $150 million. "You can't excel without daring to get close to the sun without getting burnt," he asserted.
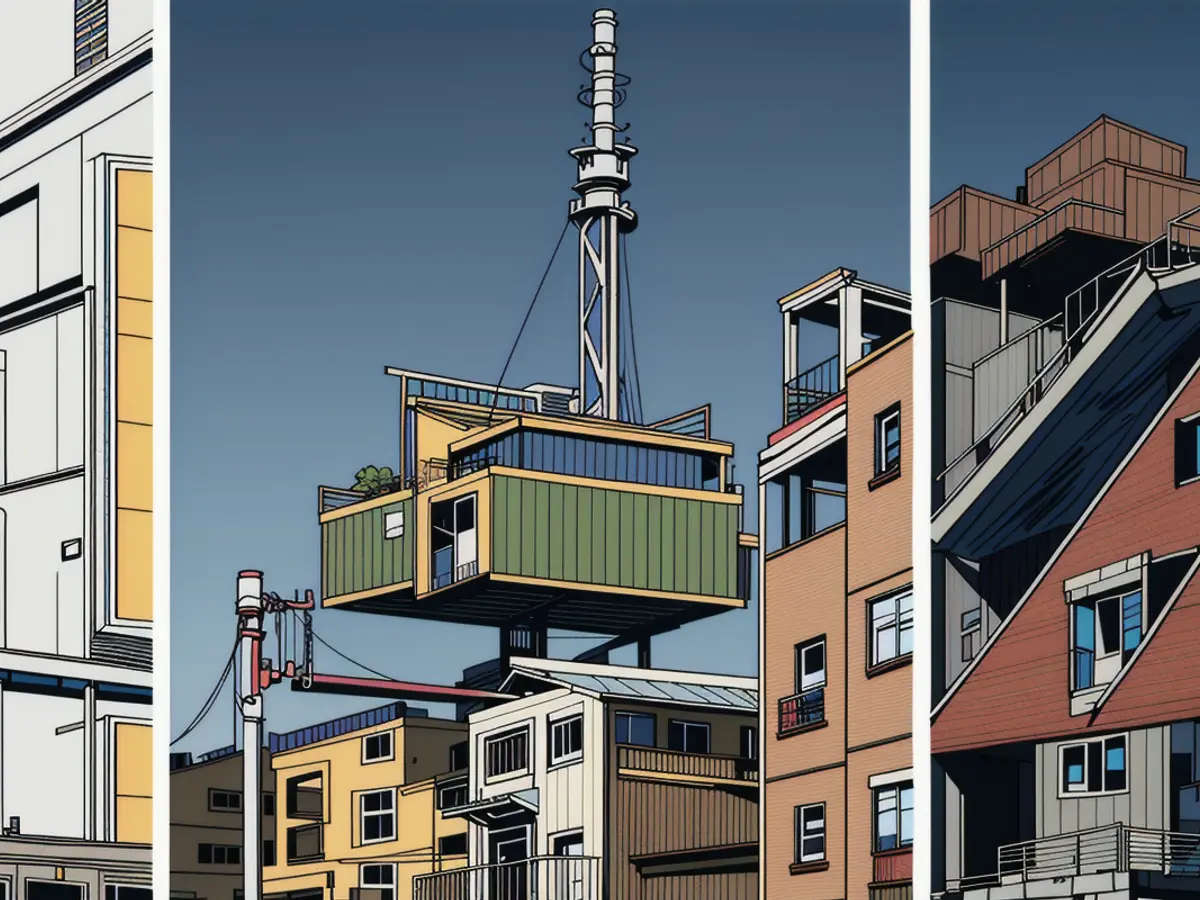
Today, Zekelman Industries, fully owned by Barry Zekelman and his brothers Alan, 62, and Clayton, 55, manufactures approximately 2.5 million tons of steel from 17 factories. Neither of his brothers performs an operational role. "I could be considered a bully in a sense," he admits. "I had to move faster than they did. I have my regrets about that...But you can't love me for my actions and then rebuke me for them."
Zekelman Industries produces all its steel pipes and tubing in North America, and Zekelman is a staunch critic of steel imports. In 2022, he agreed to pay a $975,000 fine - one of the largest fines ever imposed by the Federal Election Commission - for illegally aiding in redirecting $1.75 million in donations from one of his companies to a super PAC backing Trump, whose steel tariffs he supported (Foreign nationals are prohibited from contributing to U.S. political campaigns). This October, Zekelman filed a lawsuit against Mexico for violating trade agreements and dumping steel on the U.S. market, alleging that these violations resulted in the closure of its Long Beach, Calif., factory and the planned shutdown of a Chicago location.
Zekelman happened upon the modular housing business by happenstance after meeting Julian Bowron, who had invented a corner connecting block that could be used to join steel tubing for modular construction. The resulting room frameworks were extremely robust, and Zekelman believed it would help him market more hollow structural steel to the construction industry. He invested in Bowron's business, VectorBloc, and purportedly spent $2 million to acquire it.
Initial modular projects suffered financially. A 2016 project in Washington, D.C. as a subcontractor for short-term family housing units concluded in litigation between Z Modular and general contractor MCN, with accusations of breach of contract. Zekelman's hotel construction endeavors crumbled during the pandemic when Americans ceased traveling. "I had $300 million worth of hotel sales," says Z Modular president Mickey McNamara, a lawyer who has worked with Zekelman since 2007 and is also executive vice president of Zekelman Industries. "It would have wrecked the business." The problem: Too many projects with multiple owners in various states, making standardization nearly impossible. "I knew in my gut, and Barry knew in his gut, that wasn't the way to operate the business," McNamara states. "You need to have control over it."
Zekelman assumed control, acquiring land to construct his own apartment complexes. He claims he decreased costs by 30% between the first and second generation of the apartment complexes, with further, smaller reductions with the third and fourth, which is currently under construction. Z Modular's initial apartment complexes were three stories high; its new design features five levels, with the potential to go as high as 10. "Whenever someone engages with something, I believe there's an opportunity to save money and time," he says. "I'm not looking for home runs. I'm picking up pennies, nickels, and dimes."
The main challenge lies in capital: As a real-estate developer, Z Modular needs to purchase land, construct factories, develop buildings, and hold them as rental properties. "Until you figure out how to scale this new approach to building without a significant amount of cash, it will have limitations," says Andrew Staniforth, a former VP at Forest City Ratner who's now CEO of modular construction startup Assembly OSM.
That's why Zekelman is considering potential private equity investors or perhaps an IPO. He harbors ambitious plans for expansion to other states, or even countries, a bold counterintuitive wager even for a billionaire. "I'd like to solve the housing issue for the world," he says. "If I can build 1,000 apartments with exceptional efficiency, why can't I build 100,000 or a million? Why can't I establish a presence in Spain, Argentina, Saudi Arabia, or Africa? Why not?"
- Despite the challenges, today, even giant real estate developers like Greystar are exploring modular construction, following Zekelman's lead.
- Zekelman believes that a housing factory is not unlike a steel tubing factory, and factory-built homes can be constructed more affordably and quickly than traditional construction.
- One of Zekelman's steel plants supplies hollow structural steel to his housing factory, which exports the prefabricated apartment modules.
- Zekelman Industries' steel-based construction may offer advantages during extreme temperatures and storms, making their modular housing options more durable and potentially reducing insurance costs.
- As a billionaire and steel magnate, Zekelman is considering options to raise additional funds for Z Modular's expansion plans, such as taking the company public or partnering with a REIT or private-equity firm.